Products
Crack Fillers and Preparation & Repair
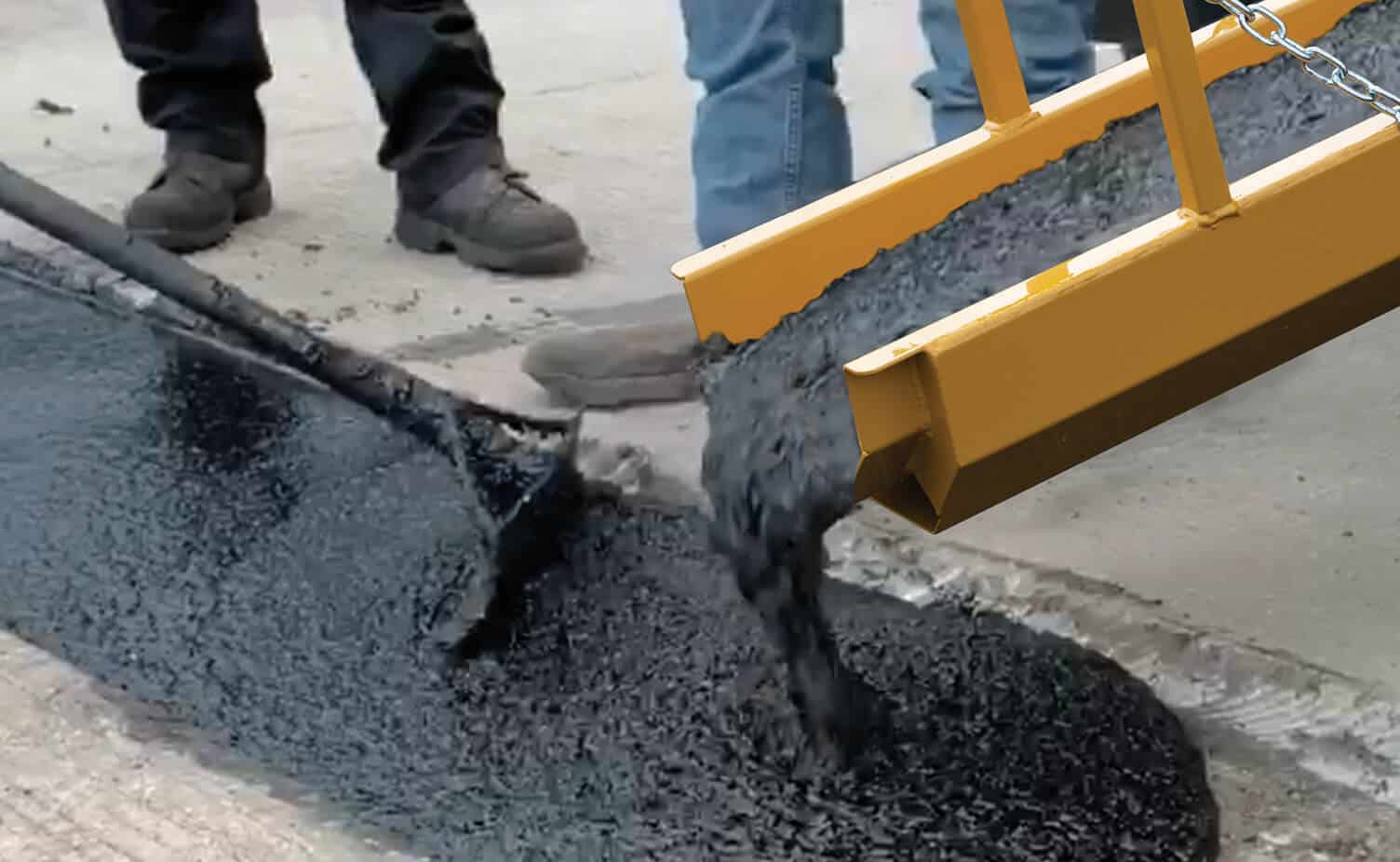
CrackMaster Mastic Roads
Hot-applied polymer modified asphalt
CrackMaster Mastic Roads is a hot-applied polymer modified asphalt mixed with specially designed aggregate and modifier combinations that is chosen to properly fill wide cracks and defects, thus allowing for prevention of water infiltration while restoring and improving traffic quality.
Download
SDS (PDF)
Spec Sheet (PDF) – English
Catalog
Description
CrackMaster Mastic Roads is a hot-applied polymer modified asphalt mixed with specially designed aggregate and modifier combinations that is chosen to properly fill wide cracks and defects, thus allowing for prevention of water infiltration while restoring and improving traffic quality.
Uses
CrackMaster Mastic Roads is designed as a long-term repair solution for wide thermal cracks, fatigue cracking, rutting and depressed, broken-up areas. CrackMaster Mastic Roads can be used on streets & roads in all climates.
Read and follow application instructions before use.
This product must be heated using indirect heating methods, either a double boiler or hot oil circulating kettle. Equipment must be capable of maintaining constant agitation to the material to keep aggregate suspended evenly.
Application
Proper surface preparation facilitates adequate adhesion and consequently the maximum life of the mastic sealant. In order for proper adhesion, the crack/joint must be free of moisture, dust, loose aggregate, and other contaminates. The substrate and air temperatures must be 40°F or above and rising. Use oil-free compressed air and heat to clean and dry the joint immediately prior to sealing.
The melting kettle should be a double boiler or conventional oil jacketed unit equipped with an agitator and temperature control devices for both the material and heat transfer oil. Carefully insert small quantities of CrackMaster Mastic Roads into the melting equipment while the agitator is turned off. Load material slowly to avoid splash back. After the initial load has reached the recommended pouring temperature, fresh material may be added to the melter as required. Melt only the material that will be used during that day. Purge material remaining in the kettle lines at the end of each sealing operation. The material may be safely reheated and can be applied using a pressure feed wand system or a pour pot.